Efficient
reduces labour costs, maximizes the growing surface with a 40ft container and increases
yield through a high plant density and optimal exposure to LED light.
A crop-to-person automated carousel enhances the benefits of the 1st generation FarmPRO. Labor costs are further reduced:
Every bench comes to you within 90 seconds, for planting, crop control, and harvesting. Each Grow Module holds 2 BenchCarousels, for a total of 4 growing layers.
Handling 1 bench is the equivalent of handling 4 gullies (irrigation gutters) at the same time.
The innovative design eliminates the need for a central corridor. Per Grow Module, this results in an industry record 86m2 growing surface (926 sq.ft) per Grow Module.
Benches allow growing all possible crop types: next to Vegetables and Herbs, you can now also grow microgreens, and much more ...
The crops have maximum exposure to light: The crops receive 200+μmol of LED light close to the canopy; on 100% of the growing surface, 100% of the time. This maximizes crop yield.
Benches can be optimized for maximum plant density Example: Genovese Basil: 220% higher planting density than a gully/gutter based system, resulting in a gross yield of 64 kg/m2/year (13 lbs/ sq.ft).
Reduced labour cost, and easy operation
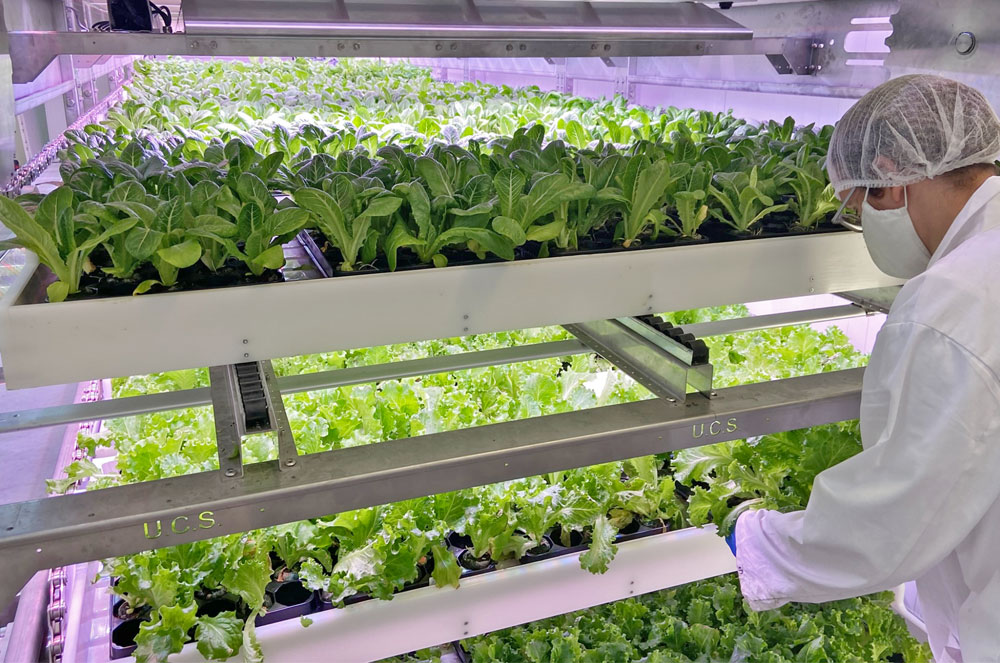
The automatic crop-to-person BenchCarousel brings any growing bench to you within 90 seconds, at the push of a button. Start harvesting any crop within seconds. Gain access to any bench to check the health of your crops.
For larger systems of 8 Grow Modules or more, we provide several options in further post-harvest automation: seeding machines, bench and tray washing machines, transplanting machines, substrate filling. We will guide you in the right automation for your business.
Industry record growing surface (86m2 / 926 sq.ft)
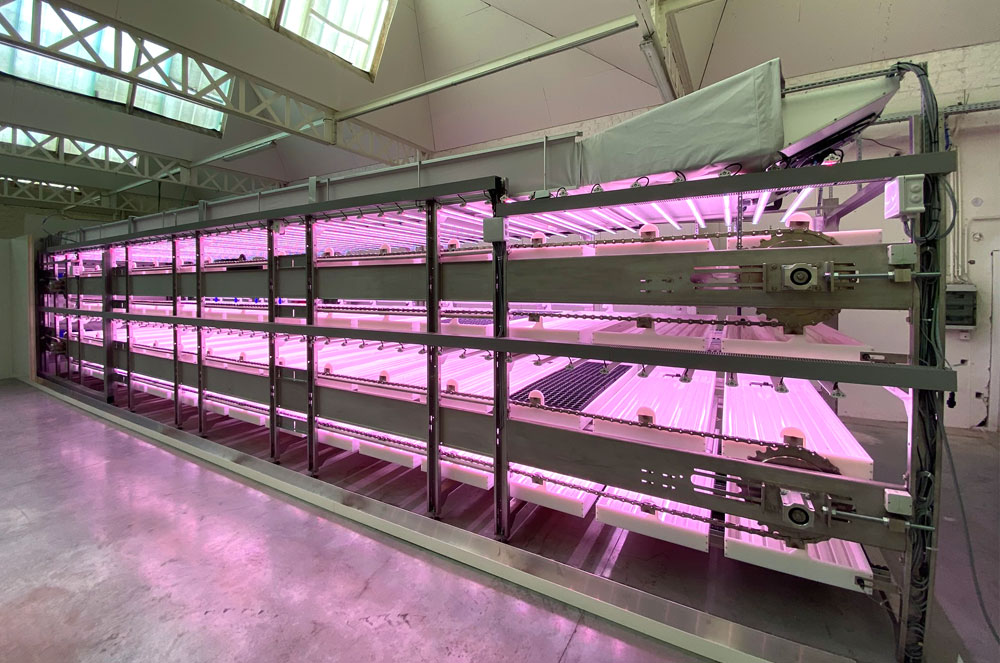
The BenchCarousel design eliminates the need for a central corridor, resulting in an industry record 86m2 (926 sq.ft) growing surface with a low CAPEX of 1800 EUR/m2 (167 EUR/sq.ft).
In reality, the most expensive 40ft container-based system is the most economical per m2 or sq.ft. growing surface: “invest in growing surface, not in buildings”.
Crops receive 100% of the light, (almost) 100% of the time
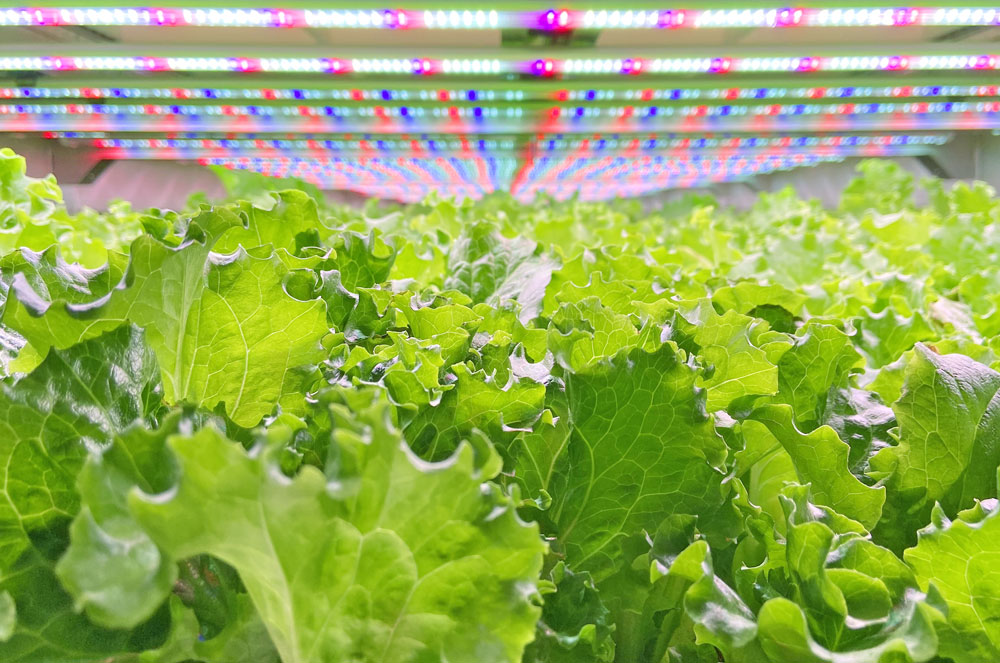
The crops have maximum exposure to light: The crops receive 200+μmol of LED light close to the canopy; on 100% of the growing surface, 100% of the time. This maximizes crop yield.
Benches can also be optimized for maximum plant density. Example: Genovese Basil: 220% higher planting density than a gully/gutter based system, resulting in a gross yield of 75 kg/m2/year (15 lbs/ sq.ft).
Scalable
Start up small, prove your business model, scale up fast
Adaptable
Every Grow Module has a separate, independent ClimateZone & Nutrient System
Example for a ModuleX-8 Plant Factory:
At the Start-Up,
the customer needs are 2 crops:
Basil : 425 kg (937 lbs) / week (ClimateZone ‘Italy’) - 4 Grow Modules used
Romaine Lettuce : 450 kg (993 lbs) / week (ClimateZone ‘France’) - 4 Grow Modules used
One Year Later,
the customer now requires 1 extra crop:
Basil : 318 kg (702 lbs) / week (ClimateZone ‘Italy’) - 3 Grow Modules used
Romaine Lettuce : 338 kg (745 lbs) / week (ClimateZone ‘France’) - 3 Grow Modules used
Microgreens : 334 kg (736 lbs) / week (ClimateZone ‘France’, with separate nutrient formula) - 2 Grow Modules used
Frequently Asked Questions
Crops
We have grown more than 200+ crops over the past 6 years, and have made a selection of crops which have given superb results in our systems. You can find the list of these crops in the Crop Guide, which can be requested on our home page.
Yes, you can grow nearly any crop in our Plant Factories and we will be happy to help you on your journey to “Grow-How”. Our Research Center is available for the development of your specific growth recipe and for contract research.
Find out more about the next steps on our Indoor Biology page where you can also contact us for more information.
Yes and No. Each crop has an optimal climate and nutrition recipe. Therefore, growing a crop at a different temperature, relative humidity, CO2 level or with a different nutrient mix can lead to Net Yields that can be lower than what we validated in our Research Center; and lower than what we list in our crop guide. To simplify the planning of your crop mix, we work with ‘Climate Zones’ and standardized nutrient formulations.
With the information of 200+ crops listed in our Crop Guide and based on your labor & electricity costs, we offer the ModuleX “feasibility calculator” free of charge, after an intake conversation. The feasibility calculator includes the intelligence of the different Climate Zones for each crop.
Next, in the business planning phase, we help you decide which crops can be grown within the same climate zone. We help you find the economic trade-off between expected yield loss and maximum factory capacity utilization.
Location
We sell our systems and provide support on-site or remotely (including start-up) all over the world. Currently, we have customers on 4 continents (North America, Europe, Asia, and Oceania).
Most of our systems (ModuleX, FarmPro, FarmFlex and FarmLab) don’t require a building and can be placed outdoors. The Large Scale Plant Factory is custom Engineered inside a new or existing stand-alone building.
Whether it is cold like in Canada, dry like in Dubai, hot like in Australia, or full of hurricanes like in the Caribbean, our Indoor Plant Factories can handle it all!
Grow Modules
The following two parameters are important to know in order to make a ROI calculation:
- Gross to Net Yield loss: How many kgs/lbs of yields do you need to remove from the crops to obtain the net yield that your customer is willing to pay for?
- Number of days that the factory is being operated: we typically calculate with 350 growing days/year, which allows for periodic cleaning and disinfection
We calculate full production costs based on the specifications which your client will need (ex. with the roots/ with the stems/ only the leaves) and your input costs (labor, water, electricity, rent, etc).
Once this information is known, the ROI will depend strongly on the sales price which varies from one region or city to another. It also varies according to the route to market (wholesale or retail, farmer’s market, …) or application (high end restaurants? Processed veggies?). If the results of the feasibility calculator, which we are offering you free of charge, make no “business sense”, you will know right away.
The ModuleX is a modular Plant Factory system that can be configured between 2 to 64 Grow Modules which are housed in 40ft freight containers. The PlantFactory is scalable with the growth of your business. One GrowModule features 86 m2 (926 sq.ft) of growing surface, yielding about 6.140 kg/year (13.536 lbs/year) of fresh vegetables. Each separate module allows for an independent climate and nutrient system, allowing your mix of crops to be adaptable to your customers’ needs. The base price is an industry-low CAPEX of 1.800 EUR/m² per growing surface (approx. 192 USD/sqft). The labor costs are reduced by the automated crop-to-person ‘BenchCarousel’. This is the most efficient solution to maximize your return on investment.
We have patented the BenchCarousel, an innovative Bench handling system that reduces labor costs, maximizes growing surface within a 40ft container and increases yield through a high plant density and an optimal exposure to LED light.
We only use new shipping containers which were made-to-order to ensure special flooring to ensure food safety and easy cleaning.
Every Module is inside a 40ft insulated shipping container (“Reefer container”) and has 4 layers. Stacking of Modules on top of each other is possible (ex. 2 modules on top of each other), however, the lengths and the number of layers within one Module are currently fixed.
Yes! You can use alternative energy for our systems. In fact, one of our customers uses 100% wind energy and also produces bio-gas from food waste.
Support
We have developed a ‘Journey to Profit’, where we offer you end-to-end support : from the planning stage, through training, startup and 1st harvest, all the way through your scale-up to a large commercial grower.
A normal startup consists of a 2-day Technical and Biological training at our Research Center in Belgium, where you learn all about indoor biology and where you get the opportunity to operate a Grow Module yourself. When the Grow Module(s) arrive at your location, our technical team will assist you in the start up and the 1st harvest.
For cities or regions with severe travel restrictions, we have reconfigured our support : everything can now be done remotely. We have now successfully educated, planned, trained, and started up our 1st FarmPro container farm REMOTELY. As a matter of fact, together with this customer/partner, we went through the entire process without having ever met in person.
We are working hard to continue to refine our remote support process, as this COVID thing will probably last a while …
Yes, each of our plant growth recipes are based on a specific seed, substrate and nutrient solution, combined with the perfect ClimateZone and Nutrient System for the crop. We are transparent about the cultivar which we recommend and the options of seed suppliers for your geographical area and we will ensure that you get the correct size and composition of the substrate. The nutrient recipe is specifically calculated based on the water analysis which our Biology team analyses for every farmer based on their location and will use nutrients which are available in your country.
We provide end-to-end support for your ‘Journey to Profit’ (see question above ”Which support do you provide?”) which are the basics to be able to operate the Plant Factory and will provide you with a manual and videos on how to operate it.
It’s important to be aware that the Plant Factory is still like a compact factory, which, in addition to growing plants, needs periodical cleaning and maintenance.
Having additional theoretical knowledge of biology is not needed (in fact, it can be counterproductive sometimes); having some hands-on experience with growing plants or with machine maintenance can be definitely a plus.